The Art of Private Customization of Precious Leather: Rediscovering the Warmth of Handcraft in the Mechanical Age

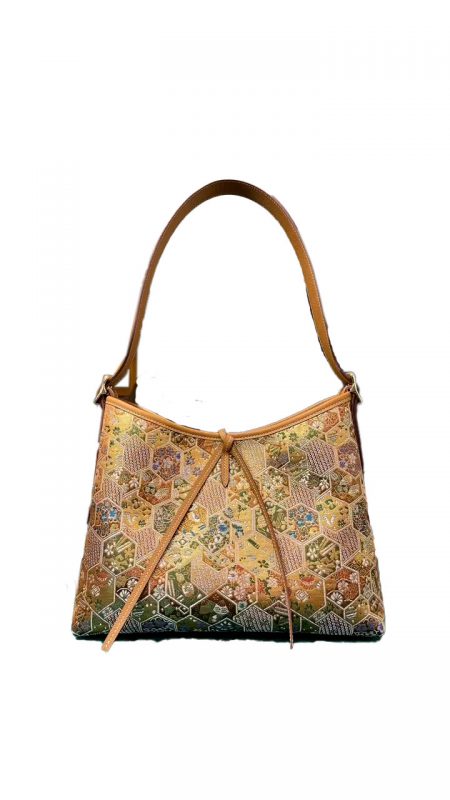
1. Leather Museum: Luxury Genes from Nature
In an era dominated by industrial assembly lines,
private customization of leather goods is a counterattack against the original craftsmanship.
We only select rare leathers certified by the world’s top raw material suppliers,
and each piece of leather carries a DNA certificate to ensure that the entire process from pores to dyes can be traced.
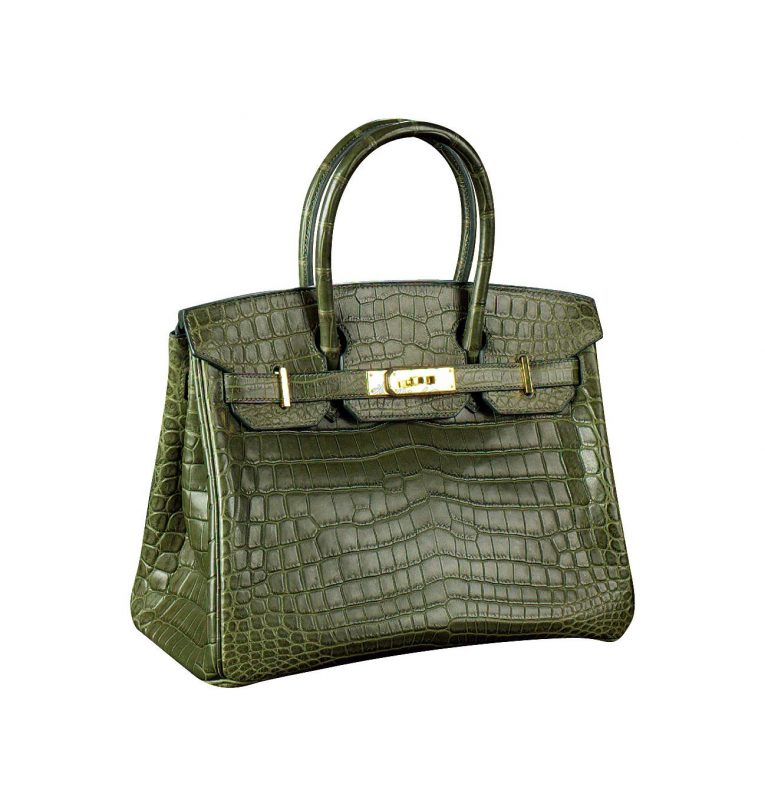
Crocodile leather | Modern expression of the totem of power
Material selection: Only 18-24 month old saltwater crocodile belly scales are used, with 6-7 bamboo knots per inch, presenting a textbook-level symmetrical aesthetic
Craftsmanship: Patented tanning technology of the French Alran workshop, 21 mineral dyeings to form a 0.01mm gradient halo
Representative work: Platinum bag replica series, 2000 copper rivets are hand-knocked to reproduce the architectural silhouette
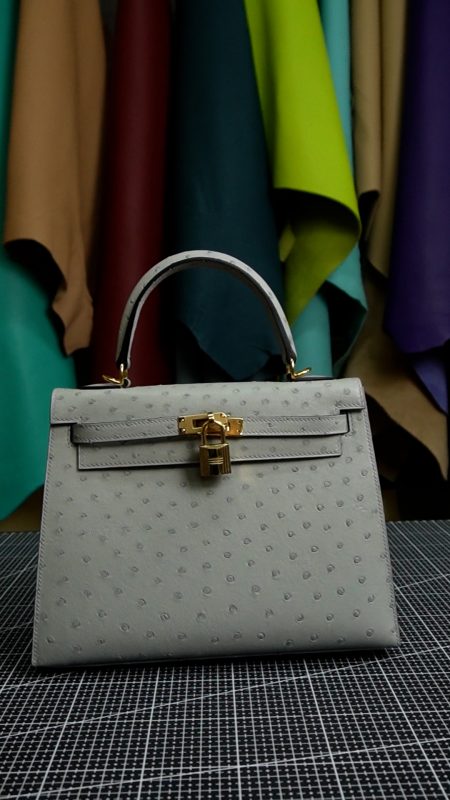
2. Ostrich leather | Soft armor of the desert king
Features: 30-50 pores per square centimeter, naturally forming a breathing diversion system
Processing: South Africa’s traditional “tea tanning method”, soaking in Rooibos black tea extract, giving it a caramel color base
Black technology: Nano-level pore sealing technology, preventing dust penetration while maintaining elasticity
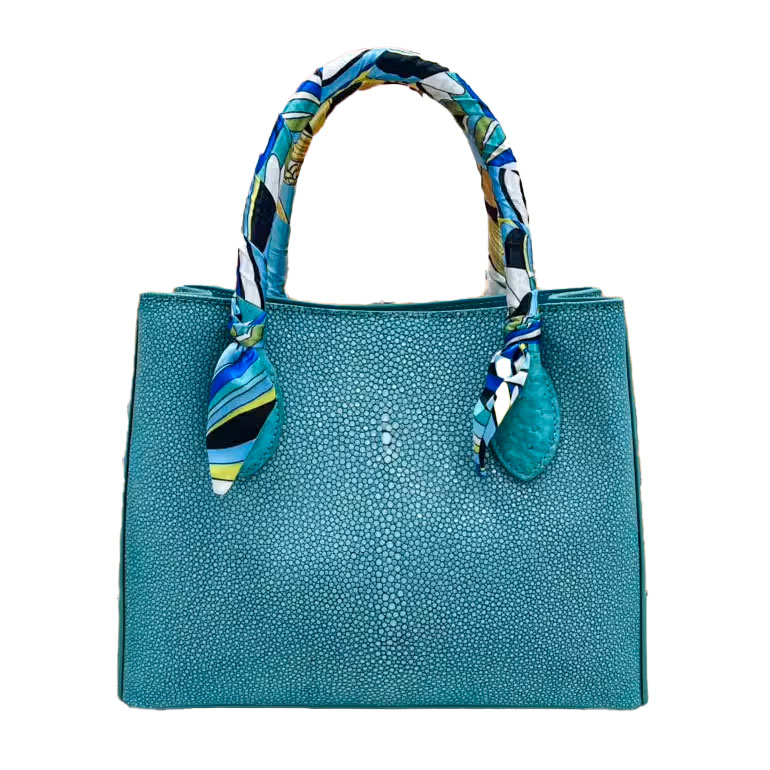
3. Pearl fish skin | Deep-sea armor reborn on land
Secret: Surface calcified particles reach Mohs hardness 4.2, comparable to lapis lazuli wear resistance
Fine processing: Hand-polished by Japanese Echizen craftsmen, each protrusion presents 16-sided reflection
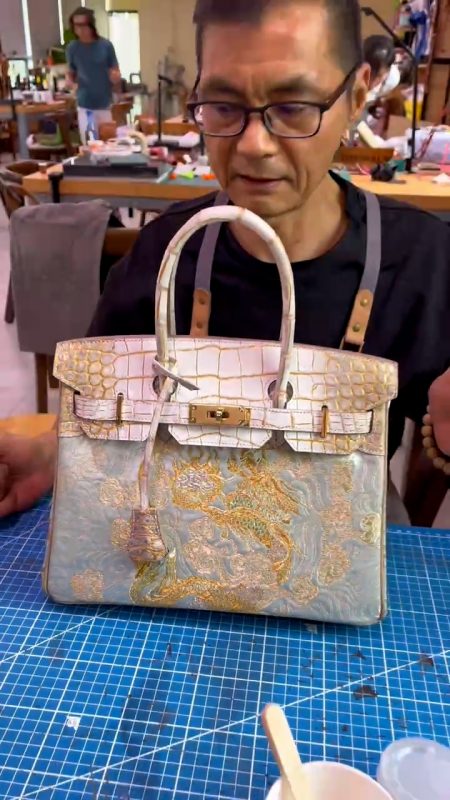
Innovation: Combining Nishijin weaving, silk relief is inlaid in the hard leather layer, and the game of hardness and softness subverts tradition
- Craftsmanship revolution: 0.02mm paranoia
- Nishijin weaving leather inlay technique
Material: Kyoto century-old workshop hand-woven brocade, 1cm² contains 1200 22K gold foil silk
Technique: Laser engraving leather inlay groove, 0.02mm error control, to achieve molecular-level combination of fabric and leather
Representative works: Kelly bag transformation, handle wrapped with Nishijin weaving “Ukiyo-e Wave” pattern
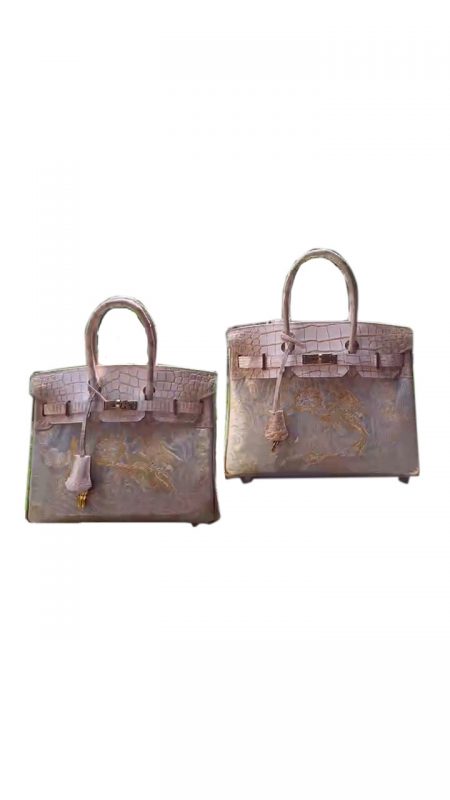
- Hermès pedigree craftsmanship
Double saddle needle method: 8.5 needles per inch, 45-degree bevel needle insertion, to ensure that the pins will not loosen for ten thousand years
Five-layer structure forging: from the inner membrane to the outer protective layer, triple temperature and humidity calibration
Secret weapon: Swiss Berna micro-air cushion system, opening and closing 100,000 times without deformation